ലേസർ വെൽഡിംഗ്
സമീപ വർഷങ്ങളിൽ, പുതിയ ഊർജ്ജ വ്യവസായത്തിന്റെ ദ്രുതഗതിയിലുള്ള വികസനത്തിന് നന്ദി, ലേസർ വെൽഡിംഗ് അതിന്റെ വേഗതയേറിയതും സുസ്ഥിരവുമായ ഗുണങ്ങൾ കാരണം മുഴുവൻ പുതിയ ഊർജ്ജ വ്യവസായത്തെയും അതിവേഗം തുളച്ചുകയറുന്നു.അവയിൽ, ലേസർ വെൽഡിംഗ് ഉപകരണങ്ങൾ മുഴുവൻ പുതിയ ഊർജ്ജ വ്യവസായത്തിലെ ആപ്ലിക്കേഷനുകളുടെ ഏറ്റവും ഉയർന്ന അനുപാതമാണ്.
വേഗത്തിലുള്ള വേഗത, വലിയ ആഴം, ചെറിയ രൂപഭേദം എന്നിവ കാരണം ജീവിതത്തിന്റെ എല്ലാ മേഖലകളിലും ലേസർ വെൽഡിംഗ് പെട്ടെന്ന് ആദ്യ തിരഞ്ഞെടുപ്പായി മാറി.സ്പോട്ട് വെൽഡുകൾ മുതൽ ബട്ട് വെൽഡുകൾ, ബിൽഡ്-അപ്പ്, സീൽ വെൽഡുകൾ വരെ ലേസർ വെൽഡിംഗ് സമാനതകളില്ലാത്ത കൃത്യതയും നിയന്ത്രണവും നൽകുന്നു.സൈനിക വ്യവസായം, മെഡിക്കൽ കെയർ, എയ്റോസ്പേസ്, 3 സി ഓട്ടോ ഭാഗങ്ങൾ, മെക്കാനിക്കൽ ഷീറ്റ് മെറ്റൽ, ന്യൂ എനർജി, മറ്റ് വ്യവസായങ്ങൾ എന്നിവയുൾപ്പെടെ വ്യാവസായിക ഉൽപ്പാദനത്തിലും നിർമ്മാണത്തിലും ഇത് ഒരു പ്രധാന പങ്ക് വഹിക്കുന്നു.
മറ്റ് വെൽഡിംഗ് സാങ്കേതികവിദ്യകളുമായി താരതമ്യപ്പെടുത്തുമ്പോൾ, ലേസർ വെൽഡിങ്ങിന് അതിന്റെ സവിശേഷമായ ഗുണങ്ങളും ദോഷങ്ങളുമുണ്ട്.
പ്രയോജനം:
1. വേഗതയേറിയ വേഗത, വലിയ ആഴം, ചെറിയ രൂപഭേദം.
2. വെൽഡിംഗ് സാധാരണ താപനിലയിലോ പ്രത്യേക വ്യവസ്ഥകളിലോ നടത്താം, വെൽഡിംഗ് ഉപകരണങ്ങൾ ലളിതമാണ്.ഉദാഹരണത്തിന്, ഒരു ലേസർ ബീം ഒരു വൈദ്യുതകാന്തിക മണ്ഡലത്തിൽ ഒഴുകുന്നില്ല.ലേസറുകൾക്ക് ഒരു വാക്വം, എയർ അല്ലെങ്കിൽ ചില വാതക പരിതസ്ഥിതികളിൽ വെൽഡ് ചെയ്യാൻ കഴിയും, കൂടാതെ ഗ്ലാസിലൂടെയോ ലേസർ ബീമിലേക്ക് സുതാര്യമായോ ഉള്ള വസ്തുക്കൾ വെൽഡ് ചെയ്യാൻ കഴിയും.
3. ഇതിന് ടൈറ്റാനിയം, ക്വാർട്സ് തുടങ്ങിയ റിഫ്രാക്റ്ററി മെറ്റീരിയലുകൾ വെൽഡ് ചെയ്യാൻ കഴിയും, കൂടാതെ നല്ല ഫലങ്ങളുള്ള സമാനമല്ലാത്ത വസ്തുക്കളെ വെൽഡ് ചെയ്യാനും കഴിയും.
4. ലേസർ ഫോക്കസ് ചെയ്ത ശേഷം, പവർ ഡെൻസിറ്റി കൂടുതലാണ്.വീക്ഷണാനുപാതം 5:1-ൽ എത്താം, ഉയർന്ന പവർ ഉപകരണങ്ങൾ വെൽഡിംഗ് ചെയ്യുമ്പോൾ 10:1 വരെ എത്താം.
5. മൈക്രോ വെൽഡിംഗ് നടത്താം.ലേസർ ബീം ഫോക്കസ് ചെയ്ത ശേഷം, ഒരു ചെറിയ സ്ഥലം ലഭിക്കുകയും കൃത്യമായി സ്ഥാപിക്കുകയും ചെയ്യാം.ഓട്ടോമേറ്റഡ് ബഹുജന ഉത്പാദനം നേടുന്നതിന് മൈക്രോ, ചെറിയ വർക്ക്പീസുകളുടെ അസംബ്ലിയിലും വെൽഡിംഗിലും ഇത് പ്രയോഗിക്കാവുന്നതാണ്.
6. ഇതിന് എത്തിച്ചേരാൻ പ്രയാസമുള്ള സ്ഥലങ്ങൾ വെൽഡ് ചെയ്യാനും വലിയ വഴക്കത്തോടെ നോൺ-കോൺടാക്റ്റ് ലോംഗ് ഡിസ്റ്റൻസ് വെൽഡിംഗ് നടത്താനും കഴിയും.പ്രത്യേകിച്ചും സമീപ വർഷങ്ങളിൽ, YAG ലേസർ പ്രോസസ്സിംഗ് സാങ്കേതികവിദ്യ ഒപ്റ്റിക്കൽ ഫൈബർ ട്രാൻസ്മിഷൻ സാങ്കേതികവിദ്യ സ്വീകരിച്ചു, ഇത് ലേസർ വെൽഡിംഗ് സാങ്കേതികവിദ്യയെ കൂടുതൽ വ്യാപകമായി പ്രോത്സാഹിപ്പിക്കാനും പ്രയോഗിക്കാനും പ്രാപ്തമാക്കി.
7. ലേസർ ബീം സമയത്തിലും സ്ഥലത്തും വിഭജിക്കാൻ എളുപ്പമാണ്, കൂടുതൽ കൃത്യമായ വെൽഡിങ്ങിനുള്ള വ്യവസ്ഥകൾ നൽകിക്കൊണ്ട് ഒന്നിലധികം സ്ഥലങ്ങളിൽ ഒരേസമയം ഒന്നിലധികം ബീമുകൾ പ്രോസസ്സ് ചെയ്യാൻ കഴിയും.
ഊനമില്ലാത്ത:
1. വർക്ക്പീസിന്റെ അസംബ്ലി കൃത്യത ഉയർന്നതായിരിക്കണം, കൂടാതെ വർക്ക്പീസിലെ ബീമിന്റെ സ്ഥാനം ഗണ്യമായി വ്യതിചലിപ്പിക്കാൻ കഴിയില്ല.കാരണം, ഫോക്കസ് ചെയ്തതിന് ശേഷമുള്ള ലേസർ സ്പോട്ട് വലുപ്പം ചെറുതും വെൽഡ് സീം ഇടുങ്ങിയതുമാണ്, ഇത് ഫില്ലർ മെറ്റൽ മെറ്റീരിയലുകൾ ചേർക്കുന്നത് ബുദ്ധിമുട്ടാണ്.വർക്ക്പീസിന്റെ അസംബ്ലി കൃത്യതയോ ബീമിന്റെ സ്ഥാനനിർണ്ണയ കൃത്യതയോ ആവശ്യകതകൾ നിറവേറ്റുന്നില്ലെങ്കിൽ, വെൽഡിംഗ് വൈകല്യങ്ങൾ ഉണ്ടാകാൻ സാധ്യതയുണ്ട്.
2. ലേസറുകളുടെയും അനുബന്ധ സംവിധാനങ്ങളുടെയും വില ഉയർന്നതാണ്, ഒറ്റത്തവണ നിക്ഷേപം വലുതാണ്.
ലിഥിയം ബാറ്ററി നിർമ്മാണത്തിലെ സാധാരണ ലേസർ വെൽഡിംഗ് വൈകല്യങ്ങൾ
1. വെൽഡിംഗ് പൊറോസിറ്റി
ലേസർ വെൽഡിങ്ങിലെ സാധാരണ തകരാറുകൾ സുഷിരങ്ങളാണ്.വെൽഡിംഗ് ഉരുകിയ കുളം ആഴവും ഇടുങ്ങിയതുമാണ്.ലേസർ വെൽഡിംഗ് പ്രക്രിയയിൽ, നൈട്രജൻ പുറത്ത് നിന്ന് ഉരുകിയ കുളത്തെ ആക്രമിക്കുന്നു.ലോഹത്തിന്റെ തണുപ്പിക്കൽ, ഘനീഭവിക്കൽ പ്രക്രിയയിൽ, താപനില കുറയുന്നതിനനുസരിച്ച് നൈട്രജന്റെ ലായകത കുറയുന്നു.ഉരുകിയ പൂൾ ലോഹം തണുക്കുമ്പോൾ, ക്രിസ്റ്റലൈസ് ചെയ്യാൻ തുടങ്ങും, , ലയിക്കുന്നത് പെട്ടെന്ന് പെട്ടെന്ന് കുറയും.ഈ സമയത്ത്, വലിയ അളവിലുള്ള വാതകം കുമിളകൾ രൂപപ്പെടുത്തും.കുമിളകളുടെ ഫ്ലോട്ടിംഗ് വേഗത മെറ്റൽ ക്രിസ്റ്റലൈസേഷൻ വേഗതയേക്കാൾ കുറവാണെങ്കിൽ, സുഷിരങ്ങൾ സൃഷ്ടിക്കപ്പെടും.
ലിഥിയം ബാറ്ററി വ്യവസായത്തിലെ പ്രയോഗങ്ങളിൽ, പോസിറ്റീവ് ഇലക്ട്രോഡിന്റെ വെൽഡിംഗ് സമയത്ത് സുഷിരങ്ങൾ ഉണ്ടാകാൻ സാധ്യതയുണ്ടെന്ന് ഞങ്ങൾ പലപ്പോഴും കണ്ടെത്തുന്നു, പക്ഷേ നെഗറ്റീവ് ഇലക്ട്രോഡിന്റെ വെൽഡിംഗ് സമയത്ത് അപൂർവ്വമായി സംഭവിക്കുന്നു.പോസിറ്റീവ് ഇലക്ട്രോഡ് അലുമിനിയം കൊണ്ടാണ് നിർമ്മിച്ചിരിക്കുന്നത് എന്നതിനാലും നെഗറ്റീവ് ഇലക്ട്രോഡ് ചെമ്പ് ഉപയോഗിച്ചുമാണ്.വെൽഡിംഗ് സമയത്ത്, ആന്തരിക വാതകം പൂർണ്ണമായും കവിഞ്ഞൊഴുകുന്നതിനുമുമ്പ് ഉപരിതലത്തിലെ ദ്രാവക അലുമിനിയം ഘനീഭവിച്ചു, വാതകം കവിഞ്ഞൊഴുകുന്നത് തടയുകയും വലുതും ചെറുതുമായ ദ്വാരങ്ങൾ ഉണ്ടാക്കുകയും ചെയ്യുന്നു.ചെറിയ സ്റ്റോമറ്റ.
മുകളിൽ സൂചിപ്പിച്ച സുഷിരങ്ങളുടെ കാരണങ്ങൾ കൂടാതെ, സുഷിരങ്ങളിൽ ബാഹ്യ വായു, ഈർപ്പം, ഉപരിതല എണ്ണ മുതലായവ ഉൾപ്പെടുന്നു. കൂടാതെ, നൈട്രജൻ വീശുന്നതിന്റെ ദിശയും കോണും സുഷിരങ്ങളുടെ രൂപീകരണത്തെ ബാധിക്കും.
വെൽഡിംഗ് സുഷിരങ്ങൾ ഉണ്ടാകുന്നത് എങ്ങനെ കുറയ്ക്കാം?
ആദ്യം, വെൽഡിങ്ങിന് മുമ്പ്, ഇൻകമിംഗ് മെറ്റീരിയലുകളുടെ ഉപരിതലത്തിലെ എണ്ണ കറകളും മാലിന്യങ്ങളും കൃത്യസമയത്ത് വൃത്തിയാക്കേണ്ടതുണ്ട്;ലിഥിയം ബാറ്ററികളുടെ ഉത്പാദനത്തിൽ, ഇൻകമിംഗ് മെറ്റീരിയൽ പരിശോധന ഒരു അനിവാര്യമായ പ്രക്രിയയാണ്.
രണ്ടാമതായി, വെൽഡിംഗ് വേഗത, ശക്തി, സ്ഥാനം മുതലായവ പോലുള്ള ഘടകങ്ങൾ അനുസരിച്ച് ഷീൽഡിംഗ് ഗ്യാസ് ഫ്ലോ ക്രമീകരിക്കണം, മാത്രമല്ല വളരെ വലുതോ ചെറുതോ ആയിരിക്കരുത്.ലേസർ പവർ, ഫോക്കസ് പൊസിഷൻ തുടങ്ങിയ ഘടകങ്ങൾക്കനുസരിച്ച് സംരക്ഷിത ക്ലോക്ക് മർദ്ദം ക്രമീകരിക്കണം, മാത്രമല്ല അത് വളരെ ഉയർന്നതോ വളരെ കുറവോ ആയിരിക്കരുത്.സംരക്ഷിത ക്ലോക്ക് നോസിലിന്റെ ആകൃതി വെൽഡിന്റെ ആകൃതി, ദിശ, മറ്റ് ഘടകങ്ങൾ എന്നിവ അനുസരിച്ച് ക്രമീകരിക്കണം, അങ്ങനെ സംരക്ഷിത വസ്ത്രത്തിന് വെൽഡിംഗ് ഏരിയയെ തുല്യമായി മൂടാൻ കഴിയും.
മൂന്നാമത്, വർക്ക്ഷോപ്പിലെ വായുവിലെ താപനില, ഈർപ്പം, പൊടി എന്നിവ നിയന്ത്രിക്കുക.ആംബിയന്റ് താപനിലയും ഈർപ്പവും അടിവസ്ത്രത്തിന്റെ ഉപരിതലത്തിലെ ഈർപ്പത്തെയും സംരക്ഷിത വാതകത്തെയും ബാധിക്കും, ഇത് ഉരുകിയ കുളത്തിലെ ജലബാഷ്പത്തിന്റെ ഉൽപാദനത്തെയും രക്ഷപ്പെടലിനെയും ബാധിക്കും.അന്തരീക്ഷ താപനിലയും ഈർപ്പവും വളരെ ഉയർന്നതാണെങ്കിൽ, അടിവസ്ത്രത്തിന്റെ ഉപരിതലത്തിലും സംരക്ഷിത വാതകത്തിലും വളരെയധികം ഈർപ്പം ഉണ്ടാകും, ഇത് വലിയ അളവിൽ ജലബാഷ്പം സൃഷ്ടിക്കുകയും സുഷിരങ്ങൾ ഉണ്ടാക്കുകയും ചെയ്യും.ആംബിയന്റ് താപനിലയും ഈർപ്പവും വളരെ കുറവാണെങ്കിൽ, അടിവസ്ത്രത്തിന്റെ ഉപരിതലത്തിലും ഷീൽഡിംഗ് വാതകത്തിലും ഈർപ്പം വളരെ കുറവായിരിക്കും, ഇത് ജലബാഷ്പത്തിന്റെ ഉത്പാദനം കുറയ്ക്കുകയും അതുവഴി സുഷിരങ്ങൾ കുറയ്ക്കുകയും ചെയ്യും;വെൽഡിംഗ് സ്റ്റേഷനിലെ താപനില, ഈർപ്പം, പൊടി എന്നിവയുടെ ടാർഗെറ്റ് മൂല്യം ഗുണനിലവാരമുള്ള ഉദ്യോഗസ്ഥർ കണ്ടെത്തട്ടെ.
നാലാമതായി, ലേസർ ഡീപ് പെനട്രേഷൻ വെൽഡിങ്ങിലെ സുഷിരങ്ങൾ കുറയ്ക്കാനോ ഇല്ലാതാക്കാനോ ബീം സ്വിംഗ് രീതി ഉപയോഗിക്കുന്നു.വെൽഡിംഗ് സമയത്ത് സ്വിംഗ് ചേർക്കുന്നത് കാരണം, വെൽഡ് സീമിലേക്കുള്ള ബീം റെസിപ്രോക്കേറ്റിംഗ് സ്വിംഗ് വെൽഡ് സീമിന്റെ ഭാഗം ആവർത്തിച്ച് വീണ്ടും ഉരുകുന്നതിന് കാരണമാകുന്നു, ഇത് വെൽഡിംഗ് പൂളിലെ ദ്രാവക ലോഹത്തിന്റെ താമസ സമയം വർദ്ധിപ്പിക്കുന്നു.അതേ സമയം, ബീമിന്റെ വ്യതിചലനം യൂണിറ്റ് ഏരിയയിലെ ചൂട് ഇൻപുട്ടും വർദ്ധിപ്പിക്കുന്നു.വെൽഡിൻറെ ആഴം-വീതി അനുപാതം കുറയുന്നു, ഇത് കുമിളകളുടെ ഉദയത്തിന് അനുകൂലമാണ്, അതുവഴി സുഷിരങ്ങൾ ഇല്ലാതാക്കുന്നു.മറുവശത്ത്, ബീമിന്റെ സ്വിംഗ് അതിനനുസരിച്ച് ചെറിയ ദ്വാരം സ്വിംഗ് ചെയ്യുന്നു, ഇത് വെൽഡിംഗ് പൂളിന് ഒരു ഉത്തേജന ശക്തി നൽകാനും വെൽഡിംഗ് പൂളിന്റെ സംവഹനവും ഇളക്കലും വർദ്ധിപ്പിക്കാനും സുഷിരങ്ങൾ ഇല്ലാതാക്കുന്നതിൽ ഗുണം ചെയ്യും.
അഞ്ചാമതായി, പൾസ് ഫ്രീക്വൻസി, പൾസ് ഫ്രീക്വൻസി എന്നത് ഒരു യൂണിറ്റ് സമയത്തിന് ലേസർ ബീം പുറപ്പെടുവിക്കുന്ന പൾസുകളുടെ എണ്ണത്തെ സൂചിപ്പിക്കുന്നു, ഇത് ഉരുകിയ കുളത്തിലെ ചൂട് ഇൻപുട്ടിനെയും താപ ശേഖരണത്തെയും ബാധിക്കും, തുടർന്ന് ഉരുകിയതിലെ താപനില ഫീൽഡിനെയും ഫ്ലോ ഫീൽഡിനെയും ബാധിക്കും. കുളം.പൾസ് ഫ്രീക്വൻസി വളരെ ഉയർന്നതാണെങ്കിൽ, അത് ഉരുകിയ കുളത്തിൽ അമിതമായ ചൂട് ഇൻപുട്ടിലേക്ക് നയിക്കും, ഇത് ഉരുകിയ കുളത്തിന്റെ താപനില വളരെ ഉയർന്നതിലേക്ക് നയിക്കും, ഉയർന്ന താപനിലയിൽ അസ്ഥിരമായ ലോഹ നീരാവി അല്ലെങ്കിൽ മറ്റ് മൂലകങ്ങൾ ഉത്പാദിപ്പിക്കുകയും സുഷിരങ്ങൾ ഉണ്ടാകുകയും ചെയ്യും.പൾസ് ഫ്രീക്വൻസി വളരെ കുറവാണെങ്കിൽ, അത് ഉരുകിയ കുളത്തിൽ വേണ്ടത്ര താപ ശേഖരണത്തിലേക്ക് നയിക്കും, ഇത് ഉരുകിയ കുളത്തിന്റെ താപനില വളരെ കുറവായിരിക്കുകയും വാതകത്തിന്റെ പിരിച്ചുവിടലും രക്ഷപ്പെടലും കുറയ്ക്കുകയും സുഷിരങ്ങൾക്ക് കാരണമാവുകയും ചെയ്യും.പൊതുവായി പറഞ്ഞാൽ, പൾസ് ഫ്രീക്വൻസി സബ്സ്ട്രേറ്റ് കനം, ലേസർ പവർ എന്നിവ അടിസ്ഥാനമാക്കി ന്യായമായ പരിധിക്കുള്ളിൽ തിരഞ്ഞെടുക്കണം, കൂടാതെ വളരെ ഉയർന്നതോ വളരെ കുറവോ ആകുന്നത് ഒഴിവാക്കുക.
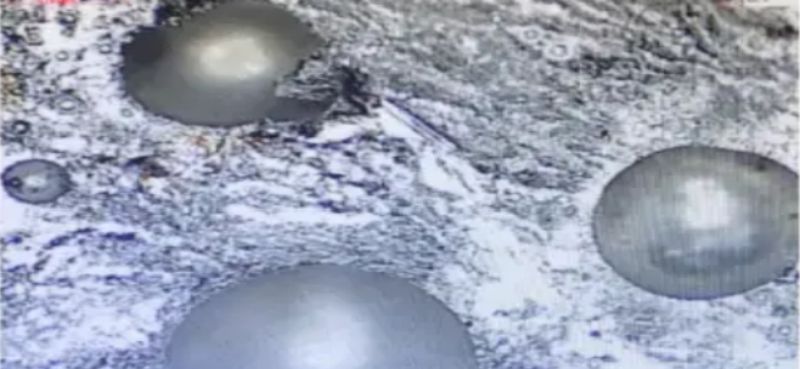
വെൽഡിംഗ് ദ്വാരങ്ങൾ (ലേസർ വെൽഡിംഗ്)
2. വെൽഡ് സ്പാറ്റർ
വെൽഡിംഗ് പ്രക്രിയയിൽ ഉണ്ടാകുന്ന സ്പാറ്റർ, ലേസർ വെൽഡിംഗ് വെൽഡിന്റെ ഉപരിതല ഗുണനിലവാരത്തെ ഗുരുതരമായി ബാധിക്കുകയും ലെൻസിനെ മലിനമാക്കുകയും നശിപ്പിക്കുകയും ചെയ്യും.പൊതുവായ പ്രകടനം ഇപ്രകാരമാണ്: ലേസർ വെൽഡിംഗ് പൂർത്തിയാക്കിയ ശേഷം, മെറ്റീരിയലിന്റെയോ വർക്ക്പീസിന്റെയോ ഉപരിതലത്തിൽ നിരവധി ലോഹ കണങ്ങൾ പ്രത്യക്ഷപ്പെടുകയും മെറ്റീരിയലിന്റെയോ വർക്ക്പീസിന്റെയോ ഉപരിതലത്തോട് ചേർന്നുനിൽക്കുകയും ചെയ്യുന്നു.ഗാൽവനോമീറ്ററിന്റെ മോഡിൽ വെൽഡിംഗ് ചെയ്യുമ്പോൾ, ഗാൽവനോമീറ്ററിന്റെ സംരക്ഷിത ലെൻസിന്റെ ഉപയോഗത്തിന് ശേഷം, ഉപരിതലത്തിൽ ഇടതൂർന്ന കുഴികൾ ഉണ്ടാകും, ഈ കുഴികൾ വെൽഡിംഗ് സ്പാറ്റർ മൂലമാണ് ഉണ്ടാകുന്നത് എന്നതാണ് ഏറ്റവും അവബോധജന്യമായ പ്രകടനം.വളരെക്കാലം കഴിഞ്ഞ്, വെളിച്ചം തടയാൻ എളുപ്പമാണ്, കൂടാതെ വെൽഡിംഗ് ലൈറ്റുമായി പ്രശ്നങ്ങൾ ഉണ്ടാകും, തൽഫലമായി, തകർന്ന വെൽഡിംഗ്, വെർച്വൽ വെൽഡിംഗ് തുടങ്ങിയ പ്രശ്നങ്ങൾ ഉണ്ടാകുന്നു.
തെറിക്കുന്നതിന്റെ കാരണങ്ങൾ എന്തൊക്കെയാണ്?
ആദ്യം, ഊർജ്ജ സാന്ദ്രത, കൂടുതൽ ഊർജ്ജ സാന്ദ്രത, സ്പാറ്റർ സൃഷ്ടിക്കുന്നത് എളുപ്പമാണ്, കൂടാതെ സ്പാറ്റർ വൈദ്യുതി സാന്ദ്രതയുമായി നേരിട്ട് ബന്ധപ്പെട്ടിരിക്കുന്നു.നൂറ്റാണ്ടുകൾ പഴക്കമുള്ള പ്രശ്നമാണിത്.കുറഞ്ഞത് ഇതുവരെ, വ്യവസായത്തിന് തെറിക്കുന്ന പ്രശ്നം പരിഹരിക്കാൻ കഴിഞ്ഞില്ല, ഇത് ചെറുതായി കുറഞ്ഞുവെന്ന് മാത്രമേ പറയാൻ കഴിയൂ.ലിഥിയം ബാറ്ററി വ്യവസായത്തിൽ, ബാറ്ററി ഷോർട്ട് സർക്യൂട്ടിന്റെ ഏറ്റവും വലിയ കുറ്റവാളി സ്പ്ലാഷിംഗ് ആണ്, പക്ഷേ ഇതിന് മൂലകാരണം പരിഹരിക്കാൻ കഴിഞ്ഞിട്ടില്ല.ബാറ്ററിയിലെ സ്പാറ്ററിന്റെ ആഘാതം പരിരക്ഷയുടെ വീക്ഷണകോണിൽ നിന്ന് മാത്രമേ കുറയ്ക്കാൻ കഴിയൂ.ഉദാഹരണത്തിന്, വെൽഡിംഗ് ഭാഗത്തിന് ചുറ്റും പൊടി നീക്കം ചെയ്യുന്ന തുറമുഖങ്ങളുടെയും സംരക്ഷിത കവറുകളുടെയും ഒരു സർക്കിൾ ചേർക്കുന്നു, കൂടാതെ സ്പാറ്ററിന്റെ ആഘാതം അല്ലെങ്കിൽ ബാറ്ററിയുടെ കേടുപാടുകൾ തടയുന്നതിന് എയർ കത്തികളുടെ നിരകൾ സർക്കിളുകളിൽ ചേർക്കുന്നു.വെൽഡിംഗ് സ്റ്റേഷന് ചുറ്റുമുള്ള പരിസ്ഥിതി, ഉൽപ്പന്നങ്ങൾ, ഘടകങ്ങൾ എന്നിവ നശിപ്പിക്കുന്നത് മാർഗങ്ങൾ തീർന്നുവെന്ന് പറയാം.
സ്പാറ്റർ പ്രശ്നം പരിഹരിക്കുന്നതിന്, വെൽഡിംഗ് എനർജി കുറയ്ക്കുന്നത് സ്പാറ്റർ കുറയ്ക്കാൻ സഹായിക്കുമെന്ന് മാത്രമേ പറയാൻ കഴിയൂ.നുഴഞ്ഞുകയറ്റം അപര്യാപ്തമാണെങ്കിൽ വെൽഡിംഗ് വേഗത കുറയ്ക്കുന്നതും സഹായിക്കും.എന്നാൽ ചില പ്രത്യേക പ്രക്രിയ ആവശ്യകതകളിൽ, ഇതിന് കാര്യമായ ഫലമില്ല.ഇത് ഒരേ പ്രക്രിയയാണ്, വ്യത്യസ്ത മെഷീനുകളും വ്യത്യസ്ത ബാച്ചുകളും മെറ്റീരിയലുകൾ തികച്ചും വ്യത്യസ്തമായ വെൽഡിംഗ് ഇഫക്റ്റുകൾ ഉണ്ട്.അതിനാൽ, പുതിയ ഊർജ്ജ വ്യവസായത്തിൽ ഒരു അലിഖിത നിയമം ഉണ്ട്, ഒരു ഉപകരണത്തിന് വെൽഡിംഗ് പാരാമീറ്ററുകളുടെ ഒരു സെറ്റ്.
രണ്ടാമതായി, പ്രോസസ്സ് ചെയ്ത മെറ്റീരിയലിന്റെയോ വർക്ക്പീസിന്റെയോ ഉപരിതലം വൃത്തിയാക്കിയില്ലെങ്കിൽ, എണ്ണ കറകളോ മലിനീകരണമോ ഗുരുതരമായ സ്പ്ലാഷുകൾക്ക് കാരണമാകും.ഈ സമയത്ത്, പ്രോസസ്സ് ചെയ്ത മെറ്റീരിയലിന്റെ ഉപരിതലം വൃത്തിയാക്കുക എന്നതാണ് ഏറ്റവും എളുപ്പമുള്ള കാര്യം.
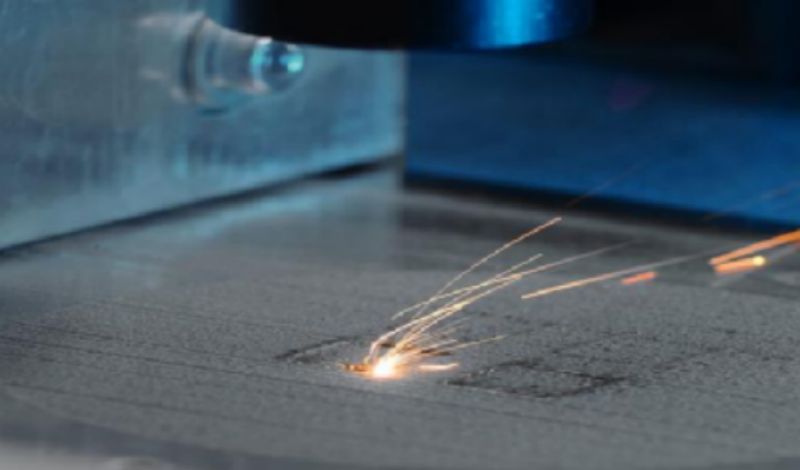
3. ലേസർ വെൽഡിങ്ങിന്റെ ഉയർന്ന പ്രതിഫലനം
സാധാരണയായി പറഞ്ഞാൽ, ഉയർന്ന പ്രതിഫലനം സൂചിപ്പിക്കുന്നത് പ്രോസസ്സിംഗ് മെറ്റീരിയലിന് ചെറിയ പ്രതിരോധശേഷി, താരതമ്യേന മിനുസമാർന്ന ഉപരിതലം, ഇൻഫ്രാറെഡ് ലേസറുകൾക്ക് കുറഞ്ഞ ആഗിരണം നിരക്ക് എന്നിവയുണ്ട്, ഇത് വലിയ അളവിൽ ലേസർ വികിരണത്തിലേക്ക് നയിക്കുന്നു, കൂടാതെ മിക്ക ലേസറുകളും ഉപയോഗിക്കുന്നു. മെറ്റീരിയൽ അല്ലെങ്കിൽ ചെറിയ അളവിലുള്ള ചെരിവ് കാരണം ലംബമായി, തിരികെ വരുന്ന ലേസർ ലൈറ്റ് ഔട്ട്പുട്ട് ഹെഡിലേക്ക് വീണ്ടും പ്രവേശിക്കുന്നു, കൂടാതെ തിരികെ വരുന്ന പ്രകാശത്തിന്റെ ഒരു ഭാഗം പോലും ഊർജ്ജം പകരുന്ന ഫൈബറിലേക്ക് യോജിപ്പിക്കുകയും ഫൈബറിനൊപ്പം ഉള്ളിലേക്ക് തിരികെ കൈമാറുകയും ചെയ്യുന്നു. ലേസറിന്റെ, ലേസറിനുള്ളിലെ പ്രധാന ഘടകങ്ങൾ ഉയർന്ന താപനിലയിൽ തുടരുന്നു.
ലേസർ വെൽഡിംഗ് സമയത്ത് പ്രതിഫലനക്ഷമത വളരെ ഉയർന്നതാണെങ്കിൽ, ഇനിപ്പറയുന്ന പരിഹാരങ്ങൾ എടുക്കാം:
3.1 ആന്റി-റിഫ്ലക്ഷൻ കോട്ടിംഗ് ഉപയോഗിക്കുക അല്ലെങ്കിൽ മെറ്റീരിയലിന്റെ ഉപരിതലത്തെ ചികിത്സിക്കുക: വെൽഡിംഗ് മെറ്റീരിയലിന്റെ ഉപരിതലത്തിൽ ആന്റി-റിഫ്ലക്ഷൻ കോട്ടിംഗ് ഉപയോഗിച്ച് പൂശുന്നത് ലേസറിന്റെ പ്രതിഫലനക്ഷമത ഫലപ്രദമായി കുറയ്ക്കും.ഈ കോട്ടിംഗ് സാധാരണയായി കുറഞ്ഞ പ്രതിഫലനക്ഷമതയുള്ള ഒരു പ്രത്യേക ഒപ്റ്റിക്കൽ മെറ്റീരിയലാണ്, അത് തിരികെ പ്രതിഫലിപ്പിക്കുന്നതിന് പകരം ലേസർ ഊർജ്ജം ആഗിരണം ചെയ്യുന്നു.നിലവിലെ കളക്ടർ വെൽഡിംഗ്, സോഫ്റ്റ് കണക്ഷൻ മുതലായവ പോലുള്ള ചില പ്രക്രിയകളിൽ, ഉപരിതലവും എംബോസ് ചെയ്യാവുന്നതാണ്.
3.2 വെൽഡിംഗ് ആംഗിൾ ക്രമീകരിക്കുക: വെൽഡിംഗ് ആംഗിൾ ക്രമീകരിക്കുന്നതിലൂടെ, ലേസർ ബീം വെൽഡിംഗ് മെറ്റീരിയലിൽ കൂടുതൽ ഉചിതമായ കോണിൽ സംഭവിക്കുകയും പ്രതിഫലനത്തിന്റെ സംഭവം കുറയ്ക്കുകയും ചെയ്യും.സാധാരണയായി, വെൽഡ് ചെയ്യേണ്ട മെറ്റീരിയലിന്റെ ഉപരിതലത്തിലേക്ക് ലംബമായി ലേസർ ബീം സംഭവം ഉണ്ടാകുന്നത് പ്രതിഫലനങ്ങൾ കുറയ്ക്കുന്നതിനുള്ള ഒരു നല്ല മാർഗമാണ്.
3.3 ഓക്സിലറി അബ്സോർബന്റ് ചേർക്കൽ: വെൽഡിംഗ് പ്രക്രിയയിൽ, പൊടി അല്ലെങ്കിൽ ദ്രാവകം പോലെയുള്ള ഒരു നിശ്ചിത അളവിലുള്ള ഓക്സിലറി അബ്സോർബന്റ് വെൽഡിലേക്ക് ചേർക്കുന്നു.ഈ അബ്സോർബറുകൾ ലേസർ ഊർജ്ജം ആഗിരണം ചെയ്യുകയും പ്രതിഫലനക്ഷമത കുറയ്ക്കുകയും ചെയ്യുന്നു.നിർദ്ദിഷ്ട വെൽഡിംഗ് മെറ്റീരിയലുകളും ആപ്ലിക്കേഷൻ സാഹചര്യങ്ങളും അടിസ്ഥാനമാക്കി ഉചിതമായ ആഗിരണം ചെയ്യേണ്ടതുണ്ട്.ലിഥിയം ബാറ്ററി വ്യവസായത്തിൽ ഇതിന് സാധ്യതയില്ല.
3.4 ലേസർ സംപ്രേഷണം ചെയ്യാൻ ഒപ്റ്റിക്കൽ ഫൈബർ ഉപയോഗിക്കുക: സാധ്യമെങ്കിൽ, റിഫ്ലക്റ്റിവിറ്റി കുറയ്ക്കുന്നതിന് വെൽഡിംഗ് സ്ഥാനത്തേക്ക് ലേസർ സംപ്രേഷണം ചെയ്യാൻ ഒപ്റ്റിക്കൽ ഫൈബർ ഉപയോഗിക്കാം.വെൽഡിംഗ് മെറ്റീരിയലിന്റെ ഉപരിതലത്തിലേക്ക് നേരിട്ട് എക്സ്പോഷർ ചെയ്യാതിരിക്കാനും പ്രതിഫലനങ്ങൾ ഉണ്ടാകുന്നത് കുറയ്ക്കാനും ഒപ്റ്റിക്കൽ നാരുകൾക്ക് ലേസർ ബീമിനെ വെൽഡിംഗ് ഏരിയയിലേക്ക് നയിക്കാനാകും.
3.5 ലേസർ പാരാമീറ്ററുകൾ ക്രമീകരിക്കൽ: ലേസർ പവർ, ഫോക്കൽ ലെങ്ത്, ഫോക്കൽ വ്യാസം തുടങ്ങിയ പരാമീറ്ററുകൾ ക്രമീകരിക്കുന്നതിലൂടെ, ലേസർ ഊർജ്ജത്തിന്റെ വിതരണം നിയന്ത്രിക്കാനും പ്രതിഫലനങ്ങൾ കുറയ്ക്കാനും കഴിയും.ചില പ്രതിഫലന സാമഗ്രികൾക്കായി, ലേസർ ശക്തി കുറയ്ക്കുന്നത് പ്രതിഫലനങ്ങൾ കുറയ്ക്കുന്നതിനുള്ള ഒരു ഫലപ്രദമായ മാർഗമായിരിക്കാം.
3.6 ഒരു ബീം സ്പ്ലിറ്റർ ഉപയോഗിക്കുക: ഒരു ബീം സ്പ്ലിറ്ററിന് ലേസർ ഊർജ്ജത്തിന്റെ ഒരു ഭാഗം ആഗിരണം ഉപകരണത്തിലേക്ക് നയിക്കാൻ കഴിയും, അതുവഴി പ്രതിഫലനങ്ങൾ ഉണ്ടാകുന്നത് കുറയ്ക്കും.ബീം സ്പ്ലിറ്റിംഗ് ഉപകരണങ്ങളിൽ സാധാരണയായി ഒപ്റ്റിക്കൽ ഘടകങ്ങളും അബ്സോർബറുകളും അടങ്ങിയിരിക്കുന്നു, ഉചിതമായ ഘടകങ്ങൾ തിരഞ്ഞെടുത്ത് ഉപകരണത്തിന്റെ ലേഔട്ട് ക്രമീകരിക്കുന്നതിലൂടെ, കുറഞ്ഞ പ്രതിഫലനക്ഷമത കൈവരിക്കാൻ കഴിയും.
4. വെൽഡിംഗ് അണ്ടർകട്ട്
ലിഥിയം ബാറ്ററി നിർമ്മാണ പ്രക്രിയയിൽ, ഏതൊക്കെ പ്രക്രിയകളാണ് അണ്ടർകട്ടിംഗിന് കാരണമാകുന്നത്?എന്തുകൊണ്ടാണ് അണ്ടർകട്ടിംഗ് സംഭവിക്കുന്നത്?നമുക്ക് അത് വിശകലനം ചെയ്യാം.
അണ്ടർകട്ട്, സാധാരണയായി വെൽഡിംഗ് അസംസ്കൃത വസ്തുക്കൾ പരസ്പരം നന്നായി സംയോജിപ്പിച്ചിട്ടില്ല, വിടവ് വളരെ വലുതാണ് അല്ലെങ്കിൽ ഗ്രോവ് പ്രത്യക്ഷപ്പെടുന്നു, ആഴവും വീതിയും അടിസ്ഥാനപരമായി 0.5 മില്ലീമീറ്ററിൽ കൂടുതലാണ്, മൊത്തം നീളം വെൽഡ് നീളത്തിന്റെ 10% ത്തിൽ കൂടുതലാണ്, അല്ലെങ്കിൽ ഉൽപ്പന്ന പ്രോസസ്സ് സ്റ്റാൻഡേർഡിനേക്കാൾ കൂടുതൽ അഭ്യർത്ഥിച്ച ദൈർഘ്യം.
മുഴുവൻ ലിഥിയം ബാറ്ററി നിർമ്മാണ പ്രക്രിയയിൽ, അണ്ടർകട്ടിംഗ് ഉണ്ടാകാനുള്ള സാധ്യത കൂടുതലാണ്, കൂടാതെ സിലിണ്ടർ കവർ പ്ലേറ്റിന്റെ സീലിംഗ് പ്രീ-വെൽഡിംഗിലും വെൽഡിംഗിലും സ്ക്വയർ അലുമിനിയം ഷെൽ കവർ പ്ലേറ്റിന്റെ സീലിംഗ് പ്രീ-വെൽഡിംഗിലും വെൽഡിംഗിലും ഇത് സാധാരണയായി വിതരണം ചെയ്യപ്പെടുന്നു.പ്രധാന കാരണം, സീലിംഗ് കവർ പ്ലേറ്റ് ഷെല്ലുമായി വെൽഡിംഗുമായി സഹകരിക്കേണ്ടതുണ്ട്, സീലിംഗ് കവർ പ്ലേറ്റും ഷെല്ലും തമ്മിലുള്ള പൊരുത്തപ്പെടുത്തൽ പ്രക്രിയ അമിതമായ വെൽഡ് വിടവുകൾ, ഗ്രോവുകൾ, തകർച്ച മുതലായവയ്ക്ക് സാധ്യതയുണ്ട്, അതിനാൽ ഇത് പ്രത്യേകിച്ച് അടിവസ്ത്രങ്ങൾക്ക് സാധ്യതയുണ്ട്. .
അപ്പോൾ എന്താണ് കുറവിന് കാരണമാകുന്നത്?
വെൽഡിങ്ങ് വേഗത വളരെ വേഗത്തിലാണെങ്കിൽ, വെൽഡിന്റെ മധ്യഭാഗത്തേക്ക് ചൂണ്ടിക്കാണിക്കുന്ന ചെറിയ ദ്വാരത്തിന് പിന്നിലുള്ള ദ്രാവക ലോഹത്തിന് പുനർവിതരണം ചെയ്യാൻ സമയമില്ല, തൽഫലമായി, വെൽഡിന് ഇരുവശത്തും ദൃഢീകരണവും അടിവരയിടുന്നു.മുകളിലുള്ള സാഹചര്യം കണക്കിലെടുത്ത്, ഞങ്ങൾ വെൽഡിംഗ് പാരാമീറ്ററുകൾ ഒപ്റ്റിമൈസ് ചെയ്യേണ്ടതുണ്ട്.ലളിതമായി പറഞ്ഞാൽ, വിവിധ പാരാമീറ്ററുകൾ പരിശോധിക്കുന്നതിനുള്ള ആവർത്തിച്ചുള്ള പരീക്ഷണങ്ങളാണ്, ഉചിതമായ പാരാമീറ്ററുകൾ കണ്ടെത്തുന്നത് വരെ DOE ചെയ്യുന്നത് തുടരുക.
2. വെൽഡിംഗ് മെറ്റീരിയലുകളുടെ അമിതമായ വെൽഡ് വിടവുകൾ, ഗ്രോവുകൾ, തകർച്ചകൾ മുതലായവ വിടവുകൾ നിറയ്ക്കുന്ന ഉരുകിയ ലോഹത്തിന്റെ അളവ് കുറയ്ക്കും, അടിവസ്ത്രങ്ങൾ ഉണ്ടാകാനുള്ള സാധ്യത കൂടുതലാണ്.ഇത് ഉപകരണങ്ങളുടെയും അസംസ്കൃത വസ്തുക്കളുടെയും ഒരു ചോദ്യമാണ്.വെൽഡിംഗ് അസംസ്കൃത വസ്തുക്കൾ ഞങ്ങളുടെ പ്രക്രിയയുടെ ഇൻകമിംഗ് മെറ്റീരിയൽ ആവശ്യകതകൾ നിറവേറ്റുന്നുണ്ടോ, ഉപകരണങ്ങളുടെ കൃത്യത ആവശ്യകതകൾ നിറവേറ്റുന്നുണ്ടോ തുടങ്ങിയവ. വിതരണക്കാരെയും ഉപകരണത്തിന്റെ ചുമതലയുള്ള ആളുകളെയും നിരന്തരം പീഡിപ്പിക്കുകയും അടിക്കുകയും ചെയ്യുക എന്നതാണ് സാധാരണ രീതി.
3. ലേസർ വെൽഡിങ്ങിന്റെ അവസാനത്തിൽ ഊർജ്ജം വളരെ വേഗത്തിൽ കുറയുകയാണെങ്കിൽ, ചെറിയ ദ്വാരം തകർന്നേക്കാം, ഇത് പ്രാദേശിക അടിവരയിടുന്നതിന് കാരണമാകുന്നു.ശക്തിയുടെയും വേഗതയുടെയും ശരിയായ പൊരുത്തത്തിന് അണ്ടർകട്ടുകളുടെ രൂപീകരണം ഫലപ്രദമായി തടയാൻ കഴിയും.പഴയ പഴഞ്ചൊല്ല് പറയുന്നതുപോലെ, പരീക്ഷണങ്ങൾ ആവർത്തിക്കുക, വിവിധ പാരാമീറ്ററുകൾ പരിശോധിക്കുക, ശരിയായ പാരാമീറ്ററുകൾ കണ്ടെത്തുന്നതുവരെ DOE തുടരുക.
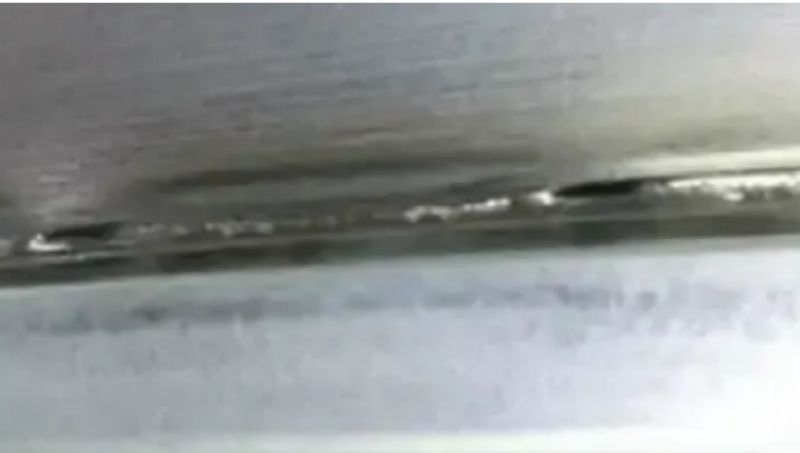
5. വെൽഡ് സെന്റർ തകർച്ച
വെൽഡിംഗ് വേഗത മന്ദഗതിയിലാണെങ്കിൽ, ഉരുകിയ കുളം വലുതും വിശാലവുമാകും, ഉരുകിയ ലോഹത്തിന്റെ അളവ് വർദ്ധിപ്പിക്കും.ഇത് ഉപരിതല പിരിമുറുക്കം നിലനിർത്തുന്നത് ബുദ്ധിമുട്ടാക്കും.ഉരുകിയ ലോഹം വളരെ ഭാരമുള്ളതായിത്തീരുമ്പോൾ, വെൽഡിന്റെ മധ്യഭാഗം മുങ്ങുകയും കുഴികളും കുഴികളും രൂപപ്പെടുകയും ചെയ്യും.ഈ സാഹചര്യത്തിൽ, മെൽറ്റ് പൂൾ തകർച്ച തടയാൻ ഊർജ്ജ സാന്ദ്രത ഉചിതമായി കുറയ്ക്കേണ്ടതുണ്ട്.
മറ്റൊരു സാഹചര്യത്തിൽ, വെൽഡിംഗ് വിടവ് സുഷിരത്തിന് കാരണമാകാതെ ഒരു തകർച്ച ഉണ്ടാക്കുന്നു.ഇത് നിസ്സംശയമായും ഉപകരണ പ്രസ്സ് ഫിറ്റിന്റെ പ്രശ്നമാണ്.
ലേസർ വെൽഡിംഗ് സമയത്ത് സംഭവിക്കാവുന്ന വൈകല്യങ്ങളെയും വ്യത്യസ്ത വൈകല്യങ്ങളുടെ കാരണങ്ങളെയും കുറിച്ചുള്ള ശരിയായ ധാരണ, അസാധാരണമായ വെൽഡിംഗ് പ്രശ്നങ്ങൾ പരിഹരിക്കുന്നതിന് കൂടുതൽ ലക്ഷ്യബോധമുള്ള സമീപനത്തെ അനുവദിക്കുന്നു.
6. വെൽഡ് വിള്ളലുകൾ
തുടർച്ചയായ ലേസർ വെൽഡിങ്ങിൽ പ്രത്യക്ഷപ്പെടുന്ന വിള്ളലുകൾ പ്രധാനമായും താപ വിള്ളലുകൾ, ക്രിസ്റ്റൽ വിള്ളലുകൾ, ദ്രവീകരണ വിള്ളലുകൾ എന്നിവയാണ്.ഈ വിള്ളലുകളുടെ പ്രധാന കാരണം വെൽഡ് പൂർണ്ണമായും ദൃഢമാകുന്നതിന് മുമ്പ് സൃഷ്ടിക്കുന്ന വലിയ ചുരുങ്ങൽ ശക്തികളാണ്.
ലേസർ വെൽഡിങ്ങിലെ വിള്ളലുകൾക്ക് ഇനിപ്പറയുന്ന കാരണങ്ങളുണ്ട്:
1. യുക്തിരഹിതമായ വെൽഡ് ഡിസൈൻ: വെൽഡിന്റെ ജ്യാമിതിയുടെയും വലുപ്പത്തിന്റെയും തെറ്റായ രൂപകൽപ്പന വെൽഡിംഗ് സ്ട്രെസ് സാന്ദ്രതയ്ക്ക് കാരണമായേക്കാം, അതുവഴി വിള്ളലുകൾ ഉണ്ടാകാം.വെൽഡിംഗ് സ്ട്രെസ് കോൺസൺട്രേഷൻ ഒഴിവാക്കാൻ വെൽഡ് ഡിസൈൻ ഒപ്റ്റിമൈസ് ചെയ്യുക എന്നതാണ് പരിഹാരം.നിങ്ങൾക്ക് ഉചിതമായ ഓഫ്സെറ്റ് വെൽഡുകൾ ഉപയോഗിക്കാം, വെൽഡ് ആകൃതി മാറ്റുക തുടങ്ങിയവ.
2. വെൽഡിംഗ് പാരാമീറ്ററുകളുടെ പൊരുത്തക്കേട്: വെൽഡിംഗ് പാരാമീറ്ററുകളുടെ തെറ്റായ തിരഞ്ഞെടുപ്പ്, വളരെ വേഗത്തിലുള്ള വെൽഡിംഗ് വേഗത, വളരെ ഉയർന്ന പവർ മുതലായവ, വെൽഡിംഗ് ഏരിയയിലെ അസമമായ താപനില മാറ്റങ്ങളിലേക്ക് നയിച്ചേക്കാം, ഇത് വലിയ വെൽഡിംഗ് സമ്മർദ്ദവും വിള്ളലുകളും ഉണ്ടാക്കുന്നു.നിർദ്ദിഷ്ട മെറ്റീരിയലും വെൽഡിംഗ് വ്യവസ്ഥകളും പൊരുത്തപ്പെടുത്തുന്നതിന് വെൽഡിംഗ് പാരാമീറ്ററുകൾ ക്രമീകരിക്കുക എന്നതാണ് പരിഹാരം.
3. വെൽഡിംഗ് ഉപരിതലത്തിന്റെ മോശം തയ്യാറെടുപ്പ്: ഓക്സൈഡുകൾ, ഗ്രീസ് മുതലായവ നീക്കം ചെയ്യുന്നതിനു മുമ്പ് വെൽഡിങ്ങ് ഉപരിതലം ശരിയായി വൃത്തിയാക്കാനും മുൻകൂട്ടി ട്രീറ്റ് ചെയ്യാനും പരാജയപ്പെടുന്നത്, വെൽഡിന്റെ ഗുണനിലവാരത്തെയും ശക്തിയെയും ബാധിക്കുകയും എളുപ്പത്തിൽ വിള്ളലുകളിലേക്ക് നയിക്കുകയും ചെയ്യും.വെൽഡിംഗ് ഏരിയയിലെ മാലിന്യങ്ങളും മാലിന്യങ്ങളും ഫലപ്രദമായി ചികിത്സിക്കുന്നുവെന്ന് ഉറപ്പാക്കാൻ വെൽഡിംഗ് ഉപരിതലം വേണ്ടത്ര വൃത്തിയാക്കുകയും പ്രീ-ട്രീറ്റ് ചെയ്യുകയും ചെയ്യുക എന്നതാണ് പരിഹാരം.
4. വെൽഡിംഗ് ഹീറ്റ് ഇൻപുട്ടിന്റെ തെറ്റായ നിയന്ത്രണം: വെൽഡിംഗ് സമയത്ത് ചൂട് ഇൻപുട്ടിന്റെ മോശം നിയന്ത്രണം, വെൽഡിംഗ് സമയത്ത് അമിതമായ താപനില, വെൽഡിംഗ് ലെയറിന്റെ അനുചിതമായ കൂളിംഗ് നിരക്ക് മുതലായവ, വെൽഡിംഗ് ഏരിയയുടെ ഘടനയിൽ മാറ്റങ്ങളിലേക്ക് നയിക്കും, ഇത് വിള്ളലുകൾക്ക് കാരണമാകും. .വെൽഡിങ്ങ് സമയത്ത് താപനിലയും ശീതീകരണ നിരക്കും നിയന്ത്രിക്കുക എന്നതാണ് പരിഹാരം, അമിത ചൂടും വേഗത്തിലുള്ള തണുപ്പും ഒഴിവാക്കുക.
5. അപര്യാപ്തമായ സ്ട്രെസ് റിലീഫ്: വെൽഡിങ്ങിന് ശേഷമുള്ള അപര്യാപ്തമായ സ്ട്രെസ് റിലീഫ് ചികിത്സ, വെൽഡിഡ് ഏരിയയിൽ മതിയായ സമ്മർദ്ദം ഒഴിവാക്കും, ഇത് എളുപ്പത്തിൽ വിള്ളലുകളിലേക്ക് നയിക്കും.ചൂട് ചികിത്സ അല്ലെങ്കിൽ വൈബ്രേഷൻ ട്രീറ്റ്മെന്റ് (പ്രധാന കാരണം) പോലെയുള്ള വെൽഡിങ്ങിനു ശേഷം ഉചിതമായ സ്ട്രെസ് റിലീഫ് ചികിത്സ നടത്തുക എന്നതാണ് പരിഹാരം.
ലിഥിയം ബാറ്ററികളുടെ നിർമ്മാണ പ്രക്രിയയെ സംബന്ധിച്ചിടത്തോളം, ഏത് പ്രക്രിയകളാണ് വിള്ളലുകൾക്ക് കൂടുതൽ സാധ്യതയുള്ളത്?
സാധാരണയായി, സിലിണ്ടർ സ്റ്റീൽ ഷെല്ലുകൾ അല്ലെങ്കിൽ അലുമിനിയം ഷെല്ലുകളുടെ സീലിംഗ് വെൽഡിംഗ്, സ്ക്വയർ അലുമിനിയം ഷെല്ലുകളുടെ സീലിംഗ് വെൽഡിംഗ് മുതലായവ സീലിംഗ് വെൽഡിംഗ് സമയത്ത് വിള്ളലുകൾ ഉണ്ടാകാൻ സാധ്യതയുണ്ട്. കൂടാതെ, മൊഡ്യൂൾ പാക്കേജിംഗ് പ്രക്രിയയിൽ, നിലവിലെ കളക്ടറുടെ വെൽഡിംഗും സാധ്യതയുണ്ട്. വിള്ളലുകളിലേക്ക്.
തീർച്ചയായും, ഈ വിള്ളലുകൾ കുറയ്ക്കുന്നതിനോ ഇല്ലാതാക്കുന്നതിനോ നമുക്ക് ഫില്ലർ വയർ, പ്രീഹീറ്റിംഗ് അല്ലെങ്കിൽ മറ്റ് രീതികൾ ഉപയോഗിക്കാം.
പോസ്റ്റ് സമയം: സെപ്റ്റംബർ-01-2023